In today’s society, the requirements for products used for newborns’ health, clothing, and use are continually increasing.
To ensure parents feel confident using these products, the infant and toddler industry is constantly researching and developing more comfortable, safe, and convenient baby nests and baby pillows.
Many parents find that the comfort and sense of security provided by baby nests, which simulate the womb environment, help babies sleep better and reduce startle reflexes.
For families that need to frequently feed and care for their children, the convenience of baby nests lies in their ability to be placed on the bedroom bed, avoiding the need to move the baby to another room or living room and preventing parents from accidentally rolling over and squeezing the baby during sleep.
Therefore, the development and use of such baby nests and baby pillows are quite friendly to new families and can also alleviate parents’ rest time.
As a professional designer and manufacturer of baby sleep products, we have a set of quality standards and inspection systems in place to ensure the stable and qualified quality of the baby nests and baby pillows we provide.
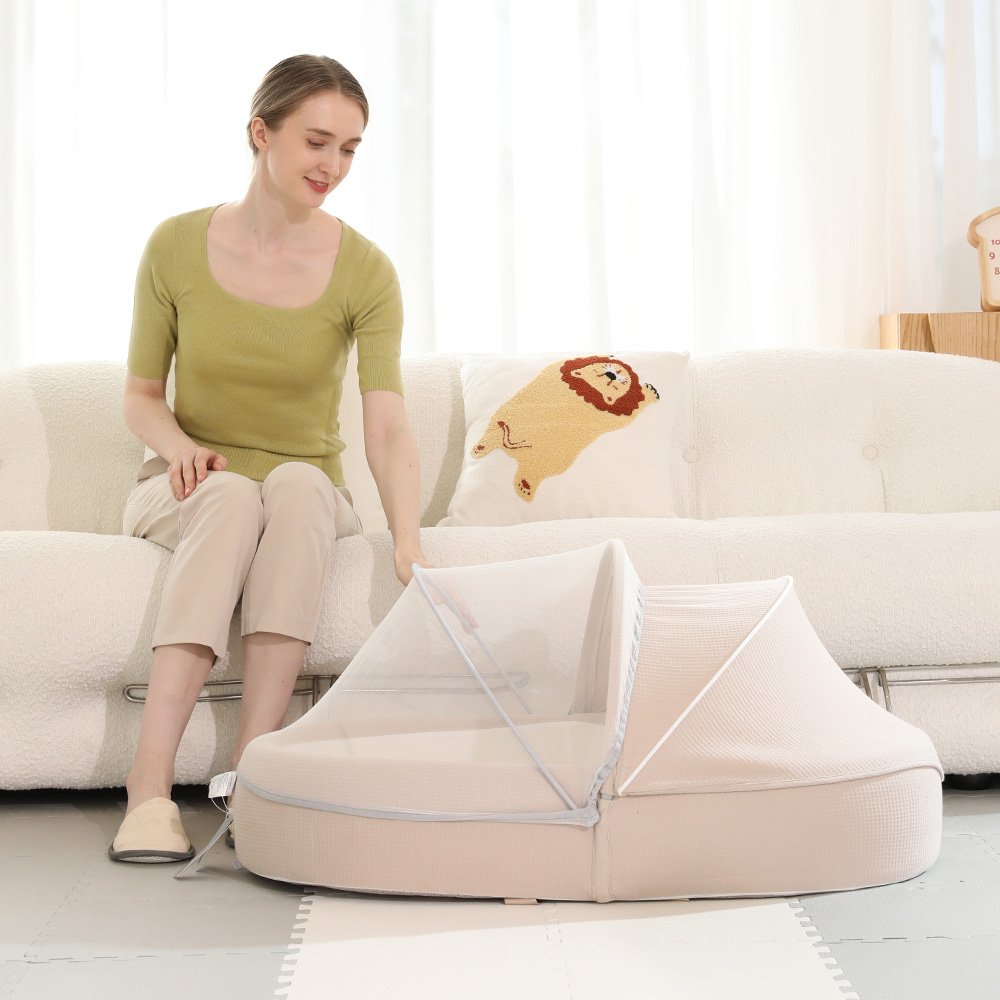
Baby Nest Lounger with Mosquito Net
Breathable and Portable Baby Nest with Mosquito Net- Newborn Lounger for 0-24 Months
Features
- Versatile use:Baby lounger can be used as a newborn baby lounger, infant lounger, sleeper baby lounger, or even a cozy spot for your baby to rest and play.
- Convenient and portable: Easy to move, making it convenient for parents to keep their baby close by at all times. It’s easy to pack and take when you’re on the go, making it a perfect portable infant lounger.
- Breathable & Easy to clean: newborn lounger is made with breathable materials. The infant lounger provides your little one with a safe and comfortable sleeping environment.
what to consider before inspecting
Before entering the infant and toddler industry, I had years of quality control experience in the large furniture industry, especially familiar with the quality control of textile-covered furniture like sofas.
By chance, I got in touch with the infant and toddler products industry.
When I first came into contact with textile products such as baby nests and baby pillows, I learned about the market segmentation of baby products based on colleagues’ introductions.
Regardless of which product you start with, you need to spend more time understanding it in detail.
Each product has inspection requirements before entering the market for sale. The primary goal of product inspection is to ensure that the quality meets the purchaser’s requirements and international standards.
For textile products that come into direct contact with the baby’s skin, such as baby nests, baby pillows, and nursing pillows, it is crucial to focus on the safety of the materials, the comfort of the raw materials, and the rationality of the design during the quality control process.
Given the variety of products, today we will mainly focus on understanding and introducing the inspection process and standards for baby nests and baby pillows.
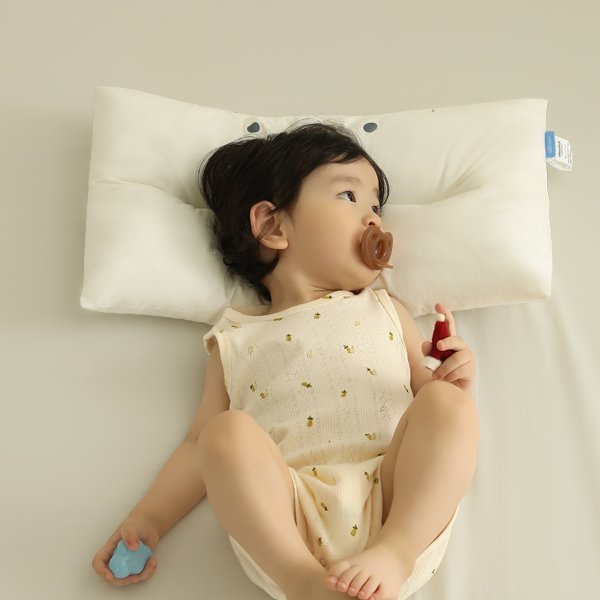
100% Cotton Animal Shape Toddler Pillows
Washable Soft Hypoallergenic Kids Toddler Pillows,100% Cotton Pillowcase
Features
- No zipper security design
- Breathable quality filling
- Cute pillowcase
- Machine washable
- Skin friendly 100% cotton fabric
Production Quality Control Process:
1. Order Review:
When put an order to the production department, we need to confirm that the custom requirements, specifications, quantity, color, packaging details, and customer order requirements are consistent.
2. Sample Comparison:
To ensure that the bulk goods meet customer requirements, we usually make 2-3 samples for customer confirmation.
The first sample is customized according to the customer’s requirements. After the customer confirms and signs it,we will keep it on file.
Before starting bulk production, we will make another pre-production sample to ensure that the materials, dimensions, patterns, and colors of the bulk production are consistent with the sample.
After the bulk production is completed, we will keep another sample for sealing. If the customer encounters quality issues with the received goods, we will take out the bulk sample for comparison, identify, and solve the problem.
Additionally, when the customer places a repeat order, we will refer to the bulk sample again to ensure consistent quality across different batches.
3. Raw Material Inspection:
After the raw materials arrive at the factory, we will conduct random inspections to check whether there are raw material test reports, confirm the composition of the fabrics and fillings, and ensure there are no harmful substances such as formaldehyde, heavy metals, or excessively high pH values.
4. Color Fastness Testing:
Fading is a common and serious issue for textile fabrics. Therefore, we must conduct color fastness tests on both raw materials and bulk goods to check whether the materials’ colors are prone to fading, avoiding the risk of color transfer to the baby’s skin during use.
5. In-line Inspection Requirements:
The factory’s hygiene standards, production environment compliance with inspection conditions, and adherence to production processes. Quality inspections are conducted before production, during semi-finished stages, and upon completion, covering both the production environment and the products.
6. Finished Product Inspection:
Mainly checking the dimensions, shape, and consistency with sample specifications; inspecting for appearance defects, stains, damage, loose threads, and other quality control issues; verifying the weight of the fillings and the accuracy of product labels and instructions.
7. Packaging:
Ensuring that packaging materials and methods comply with customer requirements to prevent damage during transportation. PE bag packaging must have anti-suffocation holes and safety warning labels.
8. Bulk Product Sampling:
After bulk goods are packed and boxed, random inspections are arranged to check the quality, specifications, packaging, and raw materials of the products to ensure consistency with the samples.
9. Functional Testing:
Conducting tests for softness, resilience, and breathability on baby pillows and baby nests.
10. Inspection Report:
After passing the inspection, the bulk goods are packed in cartons, stored in the warehouse, with hang tags and labels, and photos of non-conforming products are taken and recorded to create an inspection report for customer confirmation and backup.
11. Factory Improvement:
Non-conforming products require suppliers to repair or replace them and record the reasons for defects for further improvement.
12. Re-inspection:
If a significant proportion of non-conforming products are found in the bulk goods, an updated inspection time is scheduled after issuing the report.
13. Customer Self-Inspection or Third-Party Inspection:
We usually recommend that customers inspect the goods after our self-inspection. If customers are unable to inspect on-site, we also provide videos, pictures, and other materials for their review.
Additionally, customer-commissioned third-party inspection companies like SGS are common, and we have sufficient experience to cooperate with their efficient inspections.
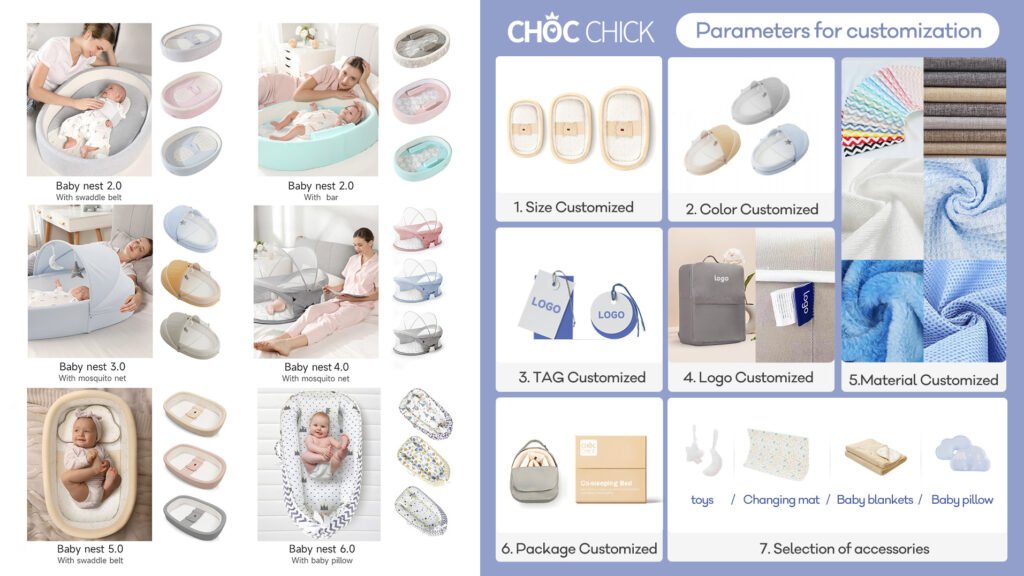
what to consider when choose a baby textile product?
Since baby nests and baby pillows serve the special target group of infants, we must pay extra attention to various aspects of safety and health for this category of textile products. Key requirements and points to consider when purchasing and using baby textile products include:
1. Safety Testing and Certification:
Whether baby textile products have passed safety testing and certification, and if there are corresponding export country testing standard certificates for exports.
2. Raw Material Selection:
Choosing materials like bamboo fiber, pure cotton, organic cotton, or poplin, which are soft, breathable, and friendly to sensitive baby skin.
3. Physical Safety:
Ensuring that buttons, zippers, and other decorations on the product are securely attached to prevent the risk of small parts being swallowed by infants. The product should have no sharp edges or hard decorations to avoid scratching the skin.
4. Continuous Testing:
Ensuring that the products are suitable for the health and safety of infants while following these precautions, parents can provide safer, healthier textiles for their babies, reducing potential health risks.
In addition to quality control throughout the production process, we strictly control the raw materials and structure during the product development stage.
We usually deeply interpret different regional infant product safety regulations such as ASTM, EN, and AU, selecting the most suitable raw materials and designing structures based on these regulations.
If you need more information about product quality control, please contact CHOCCHICK.